Recycling
The idea and impact of recycling goes beyond putting recyclable materials into a bin and having someone pick them up and discard them. We emphasize the importance of Multi-Stream Recycling versus the conventional single stream recycling model. Instead of putting all recyclable materials (paper, plastic, cardboard, glass) into the same bin, the idea behind multi-stream recycling is to separate every material that can be repurposed and reused. We are continually working with suppliers and other businesses to ensure the proper streams exist for materials that might otherwise end up in the landfill.
Our Multi-Stream Recycled Materials include:
Our Single-Stream Recycled Materials include:
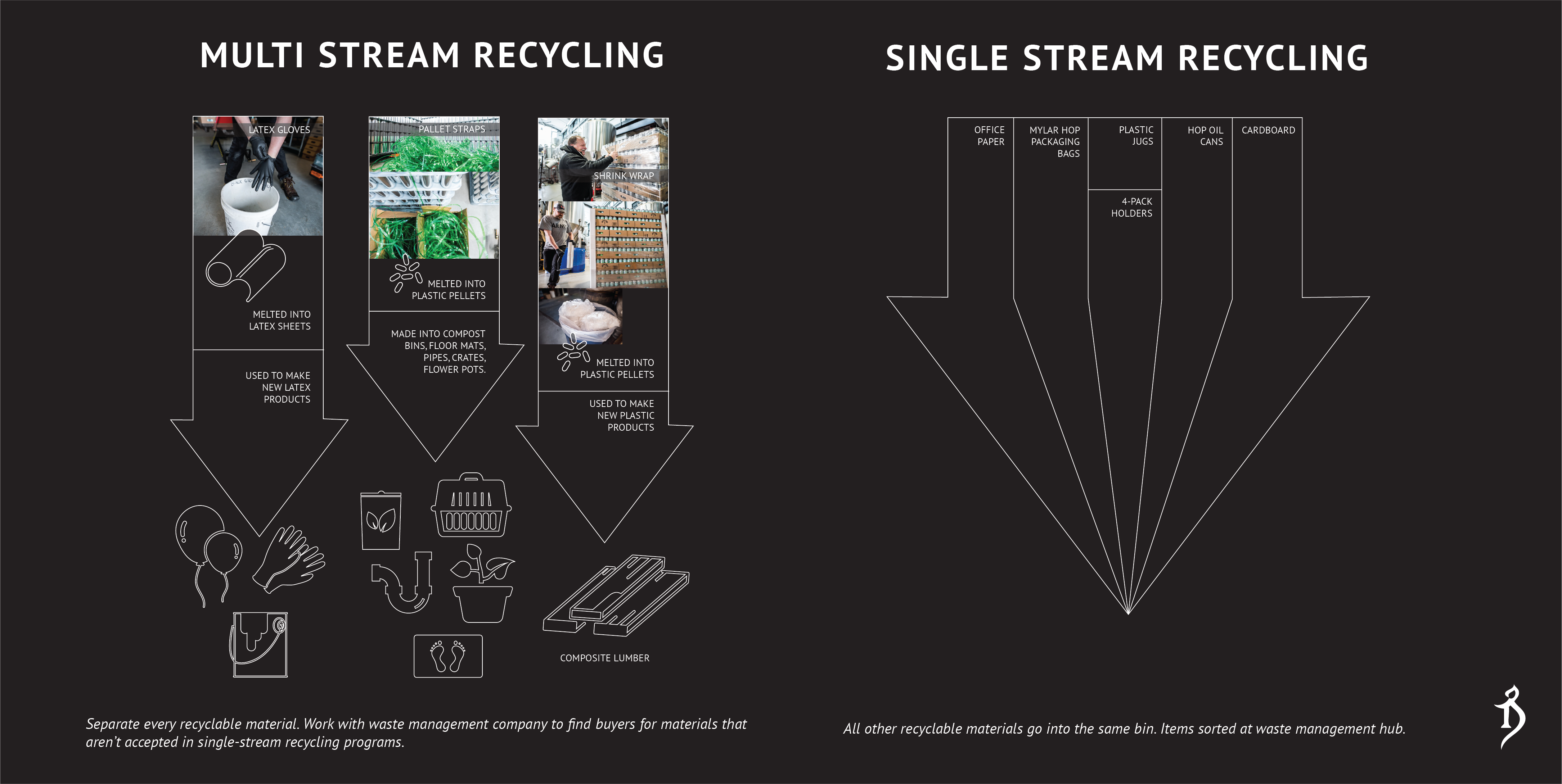
We use about 600-800 bags of grain per week between our two breweries – the largest pieces of inorganic physical waste that we generate during the brewing process. We’ve been fortunate enough to find a company that takes these grain bags and grinds them into small polypropylene pieces, melts them into pellets, then sells them to other companies to be used to make new polypro products.
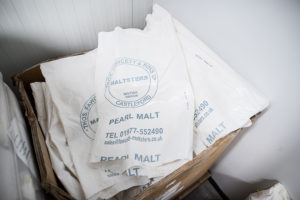
Empty grain bags ready to be picked up & recycled into other polypro products.
We aim to be 100% trash free in our facilities and continually work with our suppliers to ensure that the materials we use get reused and repurposed after their life at The Alchemist. We also work with suppliers to make sure that the materials we receive are not wrapped or packaged with contaminants that would make the material unrecyclable. These contaminants can include colored plastic labels, tape and paper.
Having a multi-stream recycling process leads to lower levels of contamination and a higher quality of recovered materials. All of the packaging and leftover materials used in the brewing process are recycled properly – some of the waste is even repurposed into energy. We have even made changes to the materials we use just to ensure we are practicing the most sustainable production possible. We used to package all of our Heady Topper four-packs in black plastic toppers. The state of Vermont ceased recycling black plastics, as they cannot be repurposed into other colored plastics. So, we switched to silver plastic toppers that can be recycled in Vermont.
Carbon Dioxide Reclamation
In an effort to reduce our emissions & reach net-zero waste, we purchased a CiCi from Earthly Labs. CiCi is a CO2 recapture machine that captures carbon dioxide generated by the brewing process. As the yeast ferments the sugars in the fermentation tanks, it generates carbon dioxide, which CiCi collects through a series of valves and pipes. The gas is dried to remove moisture, then it’s scrubbed to remove volatile organic compounds (VOCs) and other impurities, and finally it’s cooled to -30.5 °F to convert the gas to a liquid. We then store the liquid CO2 in tanks so we can use it later in the brewing process to carbonate & can the beer.
Prior to owning a CiCi, the CO2 produced by the brewing process was released into the atmosphere and we relied on purchasing CO2 from gas companies in order to carbonate and package our beer. Now, when the beer is transferred from the brite tanks to the conditioning tanks, we inject the reclaimed CO2 (which smells somewhat like our hops) into the beer and let it dissolve into solution for about 6 or 7 days. Once the beer is fully carbonated & ready for packaging, we use more reclaimed CO2 to create a pressure pocket at the top of the tank and force the beer out of the valve at the bottom of the tank at a constant rate to ensure consistency of each fill. We also use the reclaimed CO2 to purge oxygen from each can before filling it, preventing any possible oxidation/contamination at the filling stage.
To learn more, take a closer look at our CiCi in this video:
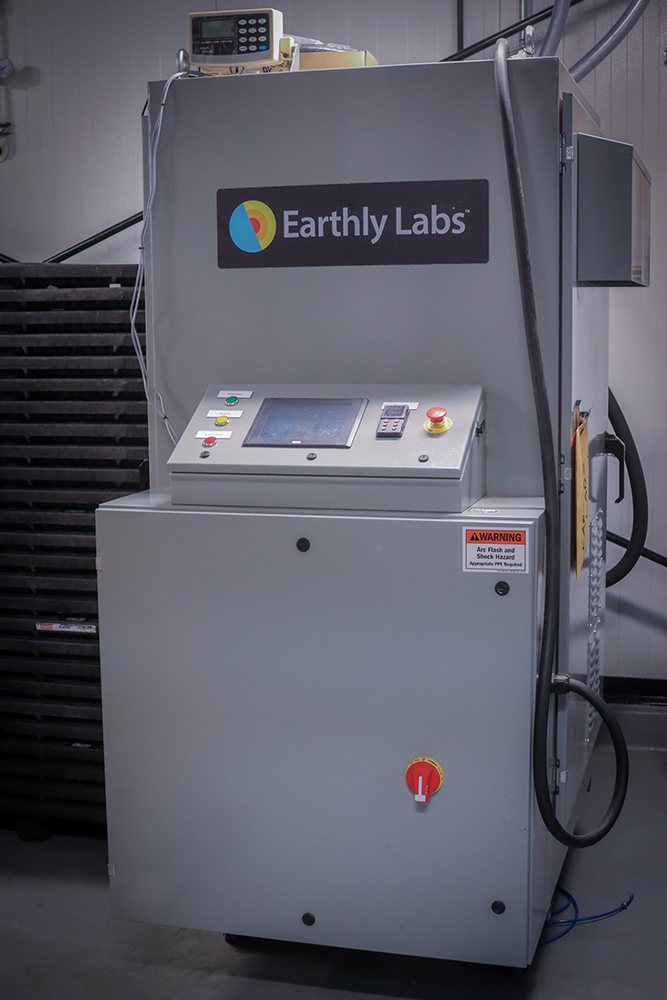
HIGH STRENGTH ORGANIC WASTE
As noted on the wastewater treatment page, the brewery residuals (tank wash, hop/yeast residues, spent grain residue, proteins & sugars, lost process beer, etc.) are collected from both of our facilities and are hauled by Evergreen Septic Services to Gebbie’s Maplehurst Farm’s anaerobic bio-digester in Greensboro. This process turns our highest-strength wastes into reusable energy or a product for farmers to use.
The biodigester breaks down the residual liquids into methane, carbon dioxide, and hydrogen. The gasses are combusted to create electricity and heat, which is then sold to the electric grid. Once digested, the remaining slurry is pumped to another tank, where an auger squeezes the effluent into liquid and solid fractions. The solids can be used for bedding cows or creating compost, while the liquid is spread on fields as fertilizer. Food scraps from our brewery’s kitchen are composted and collected by Casella’s Compost as well.
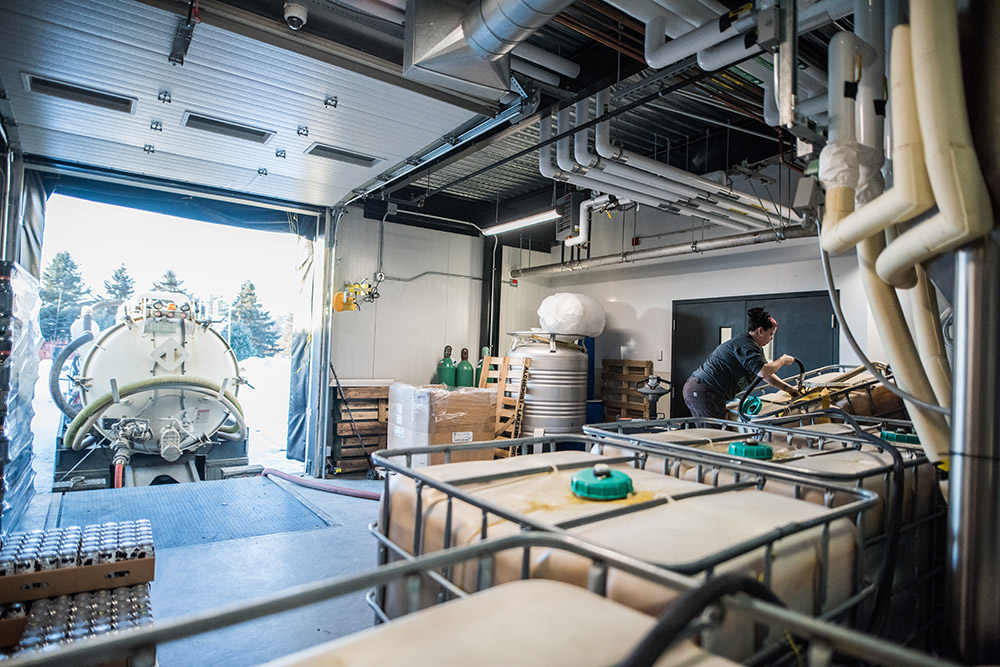
Retail
Our customer center in Stowe was designed and built with sustainable initiatives in mind. The retail space’s walls are lined with educational information about our sustainable business decisions. In addition to the solar canopies outside, expansive windows create lots of natural light and passive solar throughout the retail area.
In our retail shop, you’ll find merchandise that has been made from recycled/repurposed materials, like used malt bags that we turn into all-purpose totes. We’ve partnered with local small businesses and farmers for items such as Heady Topper soap (made with our spent grain), Heady hot sauce (made with our beer), chocolates, Cheddy Topper cheese (made with our beer) and more!
We go to great lengths to make sure that we are creating the smallest ecological footprint we can and hope to lead by example for the craft beer industry in Vermont and beyond.
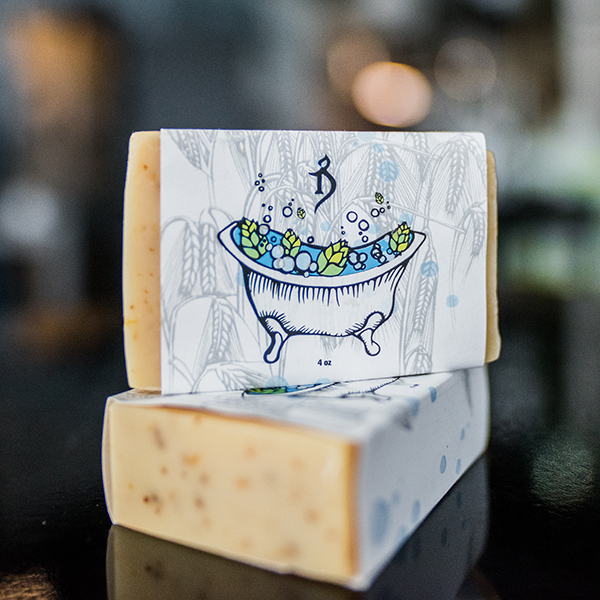
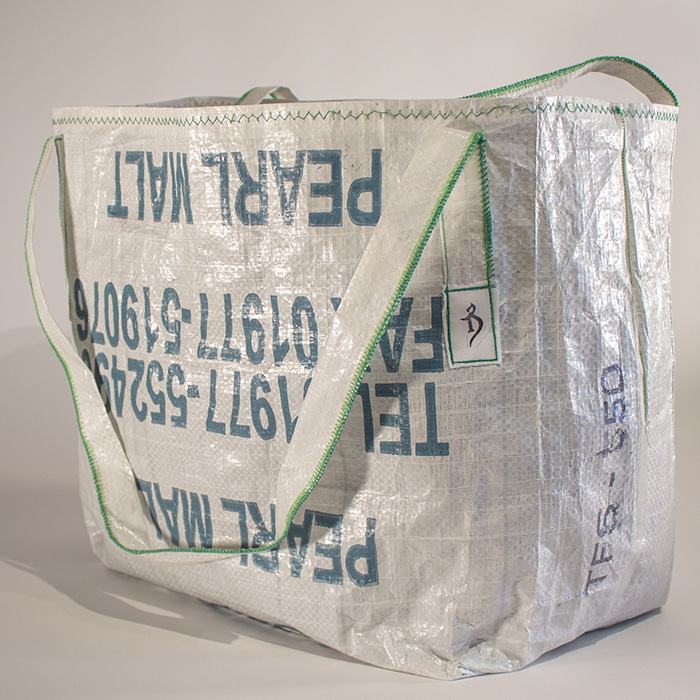
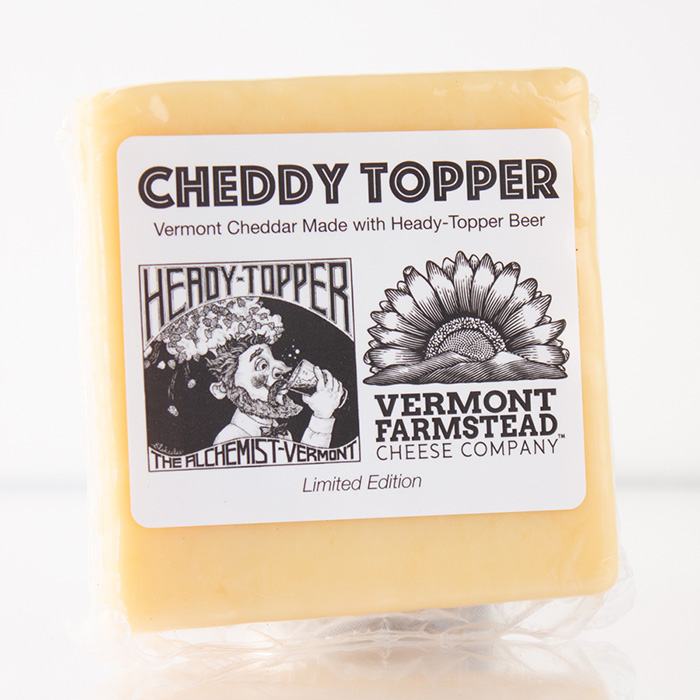
SPENT GRAIN
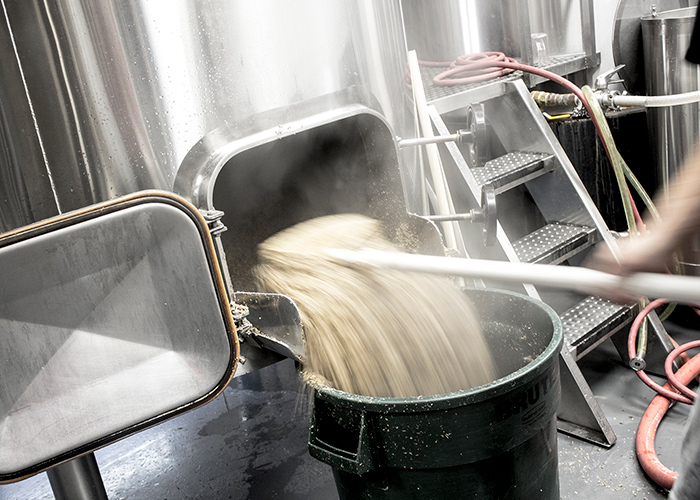
Spent grain is another byproduct of the brewing process. After the grain is mashed out, we are left with a protein- and fiber-rich product called wort. Instead of throwing away the grain, which would result in hundreds of pounds of waste every day, we collect all of our spent grain in bulk storage containers. Each week the Sweet Family Farm picks up our spent grain waste. They use the spent grain as livestock feed for their farm in Stowe, Vermont. Given the quantity of spent grain, they are also able to deliver it to many other farms around the state. Spent grain can contribute up to 85% of a brewery’s total byproduct waste.